Showing results for ( results)
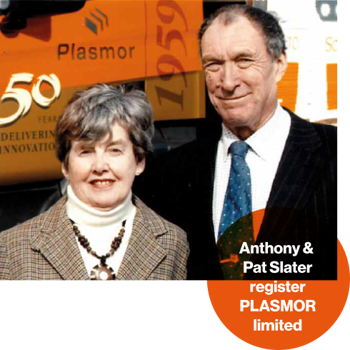
Plasmor was incorporated in 1959 on the site of an old lime-burning quarry at Womersley Road, Knottingley in Yorkshire.
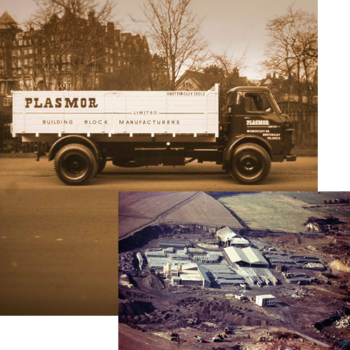
A second-hand “Egg Laying” block machine was utilised to manufacture standard breeze blocks using Furnace Bottom Ash (FBA) from Ferrybridge Coal-fired Power Station nearby. Significant growth in council house building allowed investment in the first static block plant.
A second followed in the late 1960’s, using FBA from the recently commissioned Eggborough Power Station.
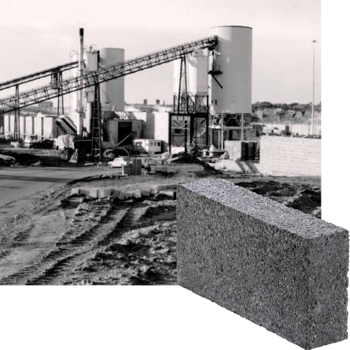
In the 1970’s, a further block plant was built at Knottingley to manufacture Architectural Facing Masonry. A second site in a family-owned former sand quarry at Great Heck near Selby was used to process the increasing amounts of FBA becoming available after the commissioning of Drax Power Station.
As demand for a wider range of building blocks grew, a large block plant was built a Great Heck in 1977 which at the time was the biggest in the UK.
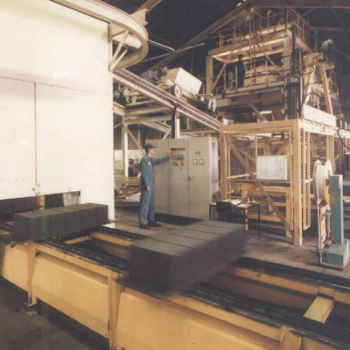
In the early 1980’s, two bolt-on acquisitions were added in quick succession; Sabey Kirby in Newton Ayclife, Co.Durham and Halton In Widnes, Cheshire.
Both were subject to significant capital investment to bring them up to Group standards including the addition of the first concrete block paving (CBP) plant at Halton in 1987.
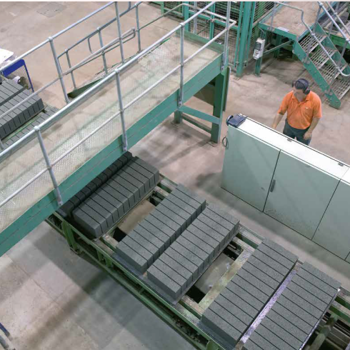
A second block plant was built at Great Heck in 1987 as the Group developed a new rail-distribution system to access the more lucrative market for blocks in the South of England.
The Great Heck site’s proximity to the East Coast Rail Line allowed the construction of fully integrated rail sidings which linked with rail distribution depots at Biggleswade in Bedfordshire and Bow in East London. The Company invested in a fleet of modified rail wagons to transport finished products to the depots.
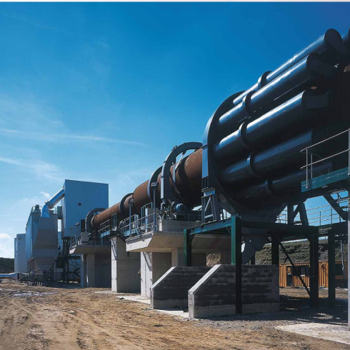
In the 1990’s, one of the block plants at Knottingley was converted into a CBP plant to meet growing demand for paving blocks. As the decade progressed, attention turned to the realisation that the supply of FBA from coal-fired power stations would diminish due to the impact they were having on climate change. Plasmor were already importing an alternative lightweight aggregate from Scandinavia which was manufactured expanded clay. A pilot rotary kiln to manufacture expanded clay aggregate was built at Knottingley in the mid-nineties.
In 1998, full- scale plant followed at Great Heck in 1998 (Kiln 1). Clay for the process was sourced from Hemingbrough Quarry near Selby
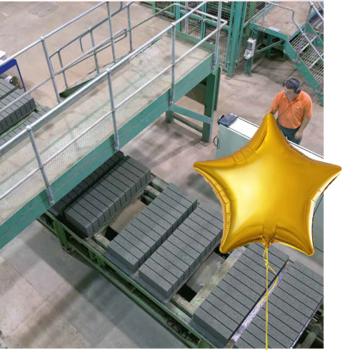
In the 2000’s, a new greenfield site was developed in Boughton, Nottinghamshire which became the home of a new hybrid Block/ CBP plant in 2003. This allowed the company to expand markets in the Midlands.
In 2005, a new large-scale block plant was built at Halton to replace the smaller plant which was demolished. An additional expanded clay aggregate plant was built at Great Heck in 2006 (Kiln 2). Escrick Quarry near York was purchased to secure clay supplies.
All at Plasmor celebrate the company’s GOLDEN anniversary in 2009
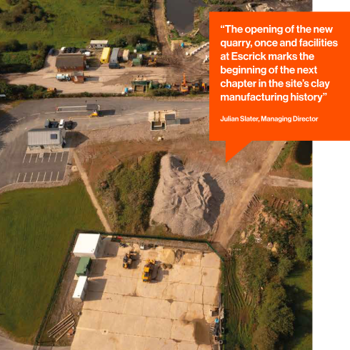
Between 2010-2020 a major program of investment in all sites was undertaken to modernise manufacturing plant, infrastructure and site facilities. Two static aggregate dry screening plants were built at Great Heck.
A new large-scale CBP plant was built at Knottingley 2018-2020. In 2021, planning permission was granted for an extension to Escrick Quarry which secured 6 million tonnes of clay for the lightweight aggregate kilns.
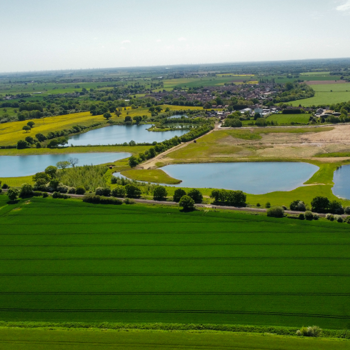
Protecting our environment and considering the future of our planet is something that can’t be ignored. Our aim is to carry on making smart decisions that consider the wider repercussions of our daily operations while ensuring the needs of the organisation and events are being met.
Discover more about our sustainability journey.